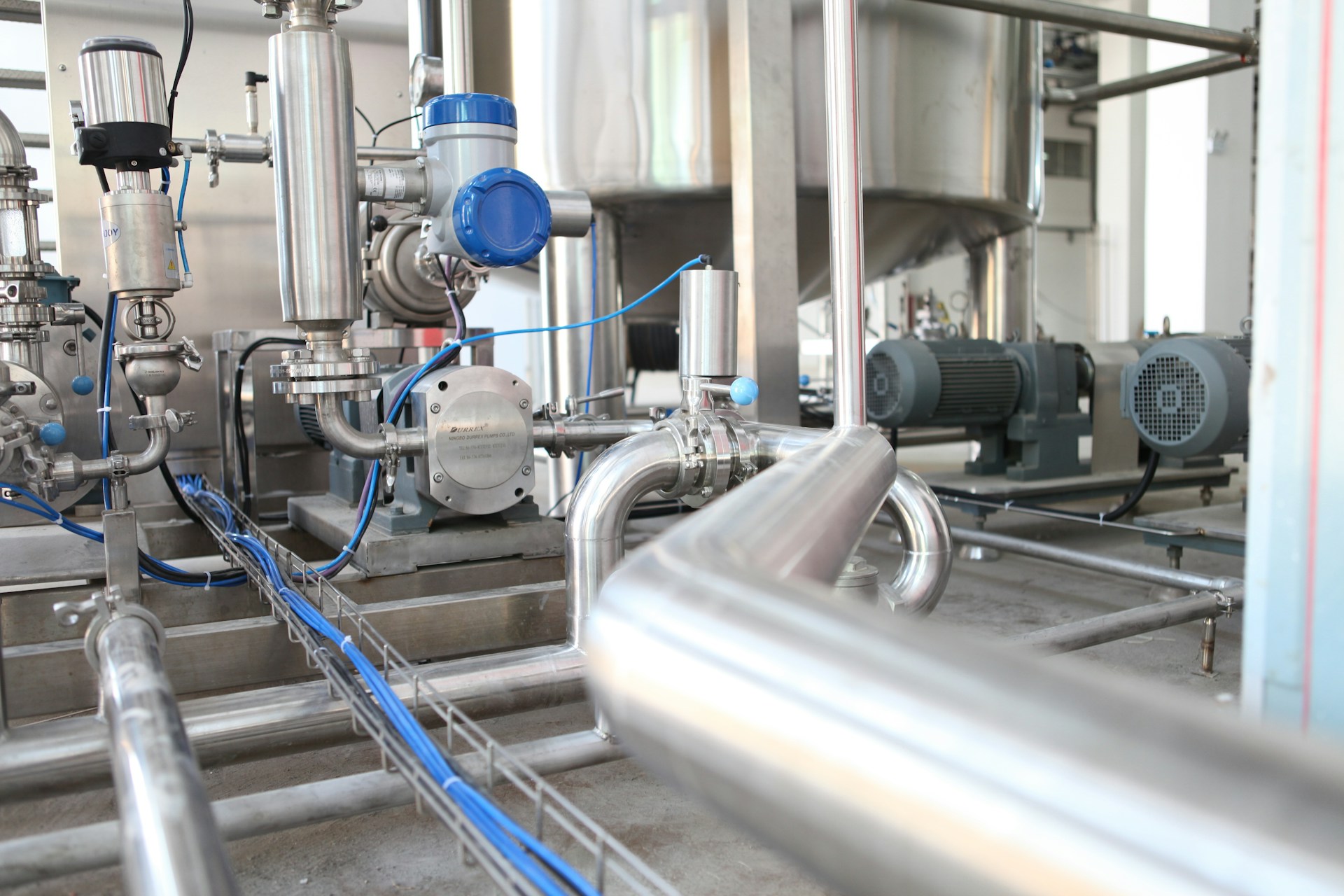
YoY revenue growth that directly impacts EBITDA
Cost visibility and overhead reduction that improves margins
Increased productivity through eliminating manual BOM data transfer
Improved BOM accuracy through real-time, bi-directional updates between CAD software and COUNTERPART
Scalable processes that support double-digit growth
Faster time to closed sales and final delivery
COUNTERPART’s proprietary add-ins for SOLIDWORKS and Autodesk Inventor offer the industry’s only bi-directional CAD ERP integrations. These integrations let you move seamlessly from CAD to production-ready BOMs without any exports or added work in Excel. Teams also save time spent solving BOM issues when parts are missing, responding to sales questions on timing and costs, or inspecting version accuracy.
ERP implementations have a bad reputation, and for good reason. They can be lengthy, costly, and disruptive. We deliver an efficient on-site implementation experience to get you up and running quickly with minimal business disturbance. After on-site implementation, our in-house support team offers responsive remote support and assistance.
Yes. COUNTERPART provides practical real-time job costing. You can see up-to-the-minute costs and labor totals for any Project
COUNTERPART’s seamless integration with SOLIDWORKS and Inventor allows the ERP to use the BOMs that are directly generated by those CAD systems. The ERP pulls together all the information you need into a format that you are already familiar with.
COUNTERPART provides a powerful search function to find old data. From Quotes created years ago to part purchase history, all historical information is easily searched and accessed for use when you need it.
COUNTERPART provides a separate Procurement Screen that lists all the parts required by engineering BOMs, shop requisitions, and parts and service orders. This allows your purchasing staff to see the entire demand for any given part, as well as giving them the tools to group and arrange the parts in any order they need. There are many streamlining tools in the application to assist the purchasing agents with creating Request for Quotes (RFQs), Purchase Orders (POs), Inventory Allocations, and other everyday tasks, minimizing their efforts, and maximizing their results.
While COUNTERPART will allow you to generate reports, you will find its display of “live work queues” is even better. You won’t have to open a report because your queue is constantly updating throughout the day as people add demands to the system. There is no need for a static view that is run daily. Just refresh the page and you get the latest demands you can directly address.
COUNTERPART was created by engineers to handle the sell-engineer-manufacture-assemble workflow in the custom manufacturing world. COUNTERPART is designed for manufacturers who create unique and customized products.
COUNTERPART uses open database technology and supports the latest Windows Operating Systems. Our Engineer To Order (ETO) ERP software Integrates seamlessly with Solidworks, PDM, Inventor, and Quickbooks. Software updates roll out every couple of months, keeping your ERP business solution software up to date and working within the Microsoft OS environment.
Yes. Your BOM needs to be fluid. In COUNTERPART, your BOM can always be altered to reflect changes. COUNTERPART allows engineers to change their BOM as needed, including items they’ve previously released. COUNTERPART will communicate any material changes to procurement for released parts, assemblies, or even an entire BOM!
COUNTERPART allows engineers to share their BOM, including changes, to Procurement throughout the design process. By ordering long lead items, and then determining the BOM requirements, engineering can release individual items, sub-assemblies, and partial BOMs to procurement once approval for purchase has been received.
COUNTERPART utilizes an easy-to-use-to-use user interface that facilitates the workflow of an engineer-to-order manufacturer. Areas like inventory, engineering, and manufacturing are accessed through the COUNTERPART homepage. You can get quick access to all reports and administrative information to keep your projects moving smoothly.
COUNTERPART provides a top-level Project and Job structure, allowing typical orders (Projects) containing broken-down deliverables and services (Jobs) to be properly arranged, grouped, and tracked. Every job is independent and sales jobs can be tagged to a serial number. You can create multiple hierarchies of order categories (essentially mini jobs) within a job.
Every role has a dedicated page that they work from for their daily tasks. These tasks are sorted generally by due dates. However, the manufacturing work queue is also sorted by readiness and availability, and the assembly work queue by availability.
COUNTERPART will show users everything they need to do, in a sortable format so they can work as they need to. If they don’t have any special sorting needs, then the default views will prioritize the list of demands/tasks for them.
Yes, and that’s the big difference. We are partners with Solidworks and Autodesk and have worked with them to develop COUNTERPART into a seamless 3D CAD integration. It becomes part of your CAD Software allowing designers to easily push BOM information to COUNTERPART.
We can work with other CAD systems as well. If you have assemblies that are not in your CAD software (such as electrical), you can directly create and revise BOMs in COUNTERPART.
If the BOM is tied to CAD, then you have to adjust it in CAD to prevent mismatches. If the BOM is NOT tied to CAD then, with the right permissions, you can revise it as needed directly through the COUNTERPART portal.
The goal is to eliminate double entry wherever possible and reduce data entry mistakes.
Yes. COUNTERPART has a dedicated filter that allows procurement to keep track of all items that have been ordered, are late, or are projected to be late. COUNTERPART allows users to track supplier performance, and identify delays before they become a problem. This helps to ensure that all required items are received by their promised delivery date or that alternative plans have been put in place.
No. COUNTERPART allows your buyers to buy material directly to a Job. You can also choose to use your available inventory first.
© 2025 Smooth Logics, LLC
This site is protected by reCAPTCHA and the Google Privacy Policy and Terms of Service apply.